In the realm of automation and robotics, servo motors are not just components—they are the backbone of precision engineering. Have you ever wondered how machines in an automotive assembly line achieve such meticulous accuracy? Or how robotic arms in surgical theaters operate with pinpoint precision? The answer often lies in the type of servo motor utilized. In this guide, we’ll delve into the critical differences between DC and AC servo motors and provide practical insights to help you choose the right type for your application.
What are Servo Motors?
Servo motors are specialized motors designed for high-accuracy control of angular or linear position, velocity, and acceleration. They are commonly found in applications that require precise motion control, such as in CNC machines, robotics, and automated manufacturing processes. Each servo motor type, whether AC or DC, is suited to different tasks and performance requirements.
DC servo motors are known for their exceptional control over movement, delivering precision at your fingertips, particularly at lower speeds. These motors are an essential component in a myriad of smaller to medium-scale applications where precision is key, ranging from intricate assembly robots to detailed artistic CNC machines.
Key Features of DC Servo Motors:
- High Torque at Low Speeds: DC servo motors excel in environments where operations start and stop frequently, requiring strong initial thrust or precise speed control during slow movements. This capability makes them highly effective for tasks that involve detailed positioning or slow, controlled operations.
- Rapid Response Time: One of the standout attributes of DC servo motors is their ability to quickly respond to command signals. This rapid response is crucial for applications that require immediate adjustments, such as in packaging machines or when used in precision insertion tasks in electronic assemblies.
- Energy Efficiency: When operating at low to medium speeds, DC servo motors are particularly efficient. This efficiency is due to their ability to maintain high torque without the need for high power input, which not only conserves energy but also reduces operational costs over time.
- Ease of Integration and Control: DC servo motors generally involve less complex drive electronics than their AC counterparts, which often translates into easier integration and control. This feature is especially beneficial for custom projects and applications where simplicity and ease of setup are paramount.
- Cost-Effectiveness: Typically, DC servo motors are more affordable compared to AC servo motors, both in terms of initial procurement and long-term maintenance. This cost-effectiveness makes them an attractive option for startups and small businesses looking to implement advanced motion control without a significant upfront investment.
DC servo motors are ideally suited for applications where precise control and efficiency are required at lower operational speeds. Their reliability, ease of use, and cost-effectiveness continue to make them a popular choice among engineers and designers in a wide array of industries. Whether for robotic arms in a production line or for the meticulous movement in laboratory automation, DC servo motors ensure that precision and control are always within reach.
Key Features of AC Servo Motors:
- Robust Power Handling: AC servo motors are capable of achieving high torque and speed, which is essential for applications that require rapid and powerful motion. This high power handling capability ensures that they can drive machinery with demanding kinetic profiles, such as heavy-duty industrial automation systems or high-speed packaging lines.
- Enhanced Durability: Built to last, AC servo motors are designed with durability at the forefront. They often feature a brushless design, which not only minimizes mechanical wear but also reduces maintenance needs. This is especially beneficial in harsh industrial conditions where exposure to dust, debris, or corrosive elements is common.
- Exceptional Efficiency and Speed: These motors are highly efficient at converting electrical energy into mechanical power, achieving superior performance with less energy consumption. AC servo motors can operate at very high speeds, making them ideal for applications where speed is as crucial as power, such as in CNC machining centers and textile manufacturing.
- Precision Control with High Dynamic Response: Despite their robust power, AC servo motors excel in applications requiring precision. They offer a high dynamic response, which means they can quickly react to changes in load and velocity. This feature is crucial for precision tasks such as robotic painting or assembly operations where exact movements are critical.
- Versatility in Applications: The adaptability of AC servo motors to various control technologies makes them versatile for a broad range of industrial applications. Whether it’s complex multi-axis systems for aerospace engineering or simple single-axis setups for conveyor belts, AC servo motors can be configured to meet diverse operational demands.
- Low Maintenance Requirements: The inherent design of AC servo motors means they come with fewer parts that are prone to wear, such as brushes. This leads to lower maintenance requirements and downtime, thereby enhancing productivity and reducing lifecycle costs.
AC servo motors stand out as the powerhouse among servo motor types, making them the preferred choice for applications that demand both high power output and extended operational longevity. These motors are engineered to operate on alternating current, which allows them to handle higher power loads and sustain continuous operation over long periods without degradation in performance. This makes AC servo motors particularly well-suited to challenging industrial environments where reliability and durability are critical.
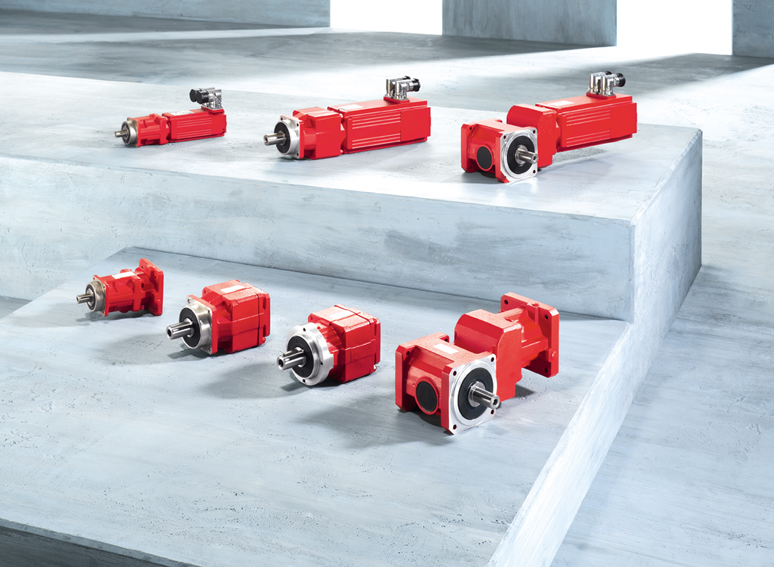
Selecting the Right Servo Motor
When choosing a servo motor, consider the specific needs of your project:
- Operational Environment: Factor in the environmental conditions as dust, moisture, and temperature can impact motor performance.
- Load Requirements: Analyze both static and dynamic loads to determine which motor type offers the best performance under expected conditions.
- Complexity of Control: Determine the complexity of the control system required. Simpler systems often align well with DC motors, whereas complex applications might benefit from the capabilities of AC motors.
At American Electric Motors, we have over 50 years of expertise in providing high-quality servo motors tailored to meet a diverse range of industrial needs. Our team is dedicated to helping you select the perfect motor solution that enhances efficiency and reliability in your applications.
Let’s Connect
For more detailed information or to consult with one of our experts, visit our website or contact American Electric Motors today. Dive into the world of high-precision engineering with us, and let’s ensure your operations are powered by the best technology available. Don’t forget to follow us on social media and share this article to help spread the word about the transformative power of the right servo motors!